Not much shop time today, save for simply putting a second coat on those two parts.
So I dug around in my camera cards, and found something from much earlier this year, that I'd been meaning to post after the whole marker is done.
Customer sent in a Carter "Boxgun" stock-classer, and like many Carters, it has a "palm swell" grip. It accepts standard .45 style grip panels, but they don't really fit the profile.
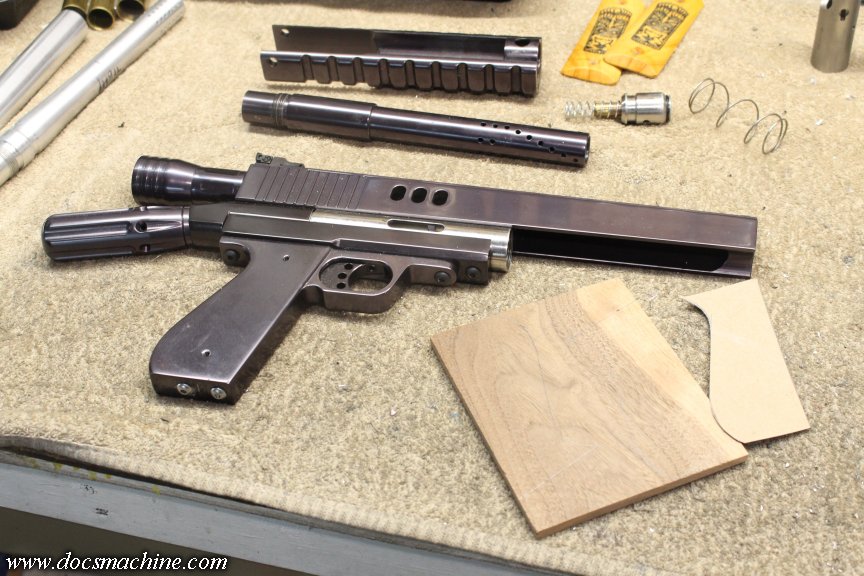
So, I made a cardboard pattern for the grip shape, and traced that to a small slab of Walnut.
This I rough-sawed out with the jigsaw...
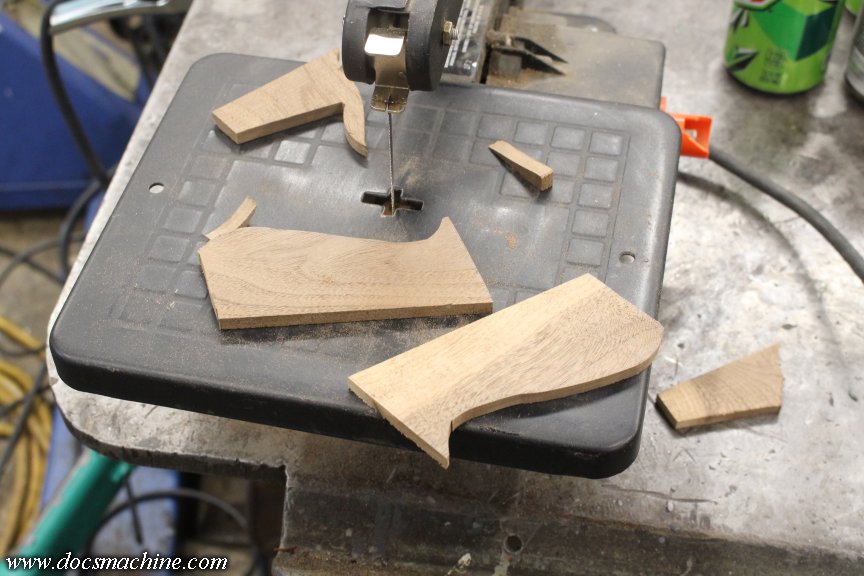
And shaped and smoothed the pair on the belt sander.
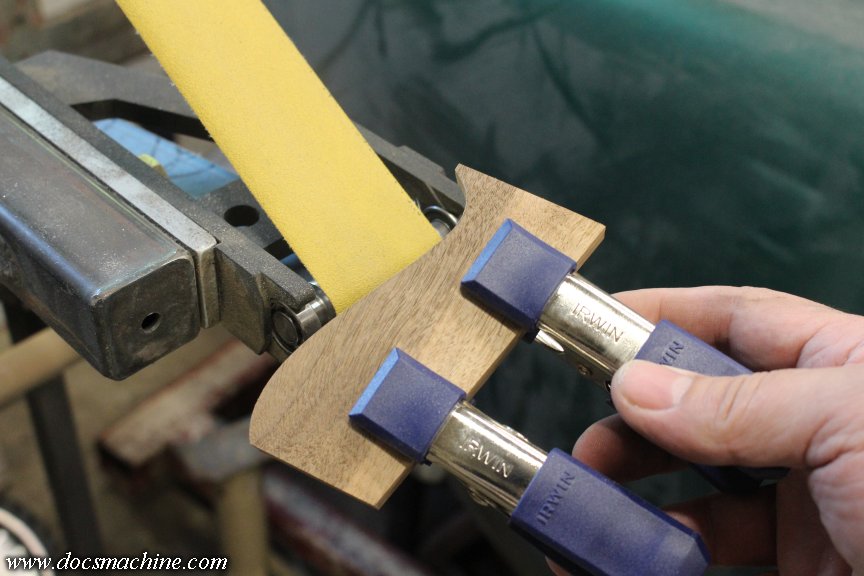
It usually takes a few test-fits and tries to get the shape just right- and the patience to not go too far.
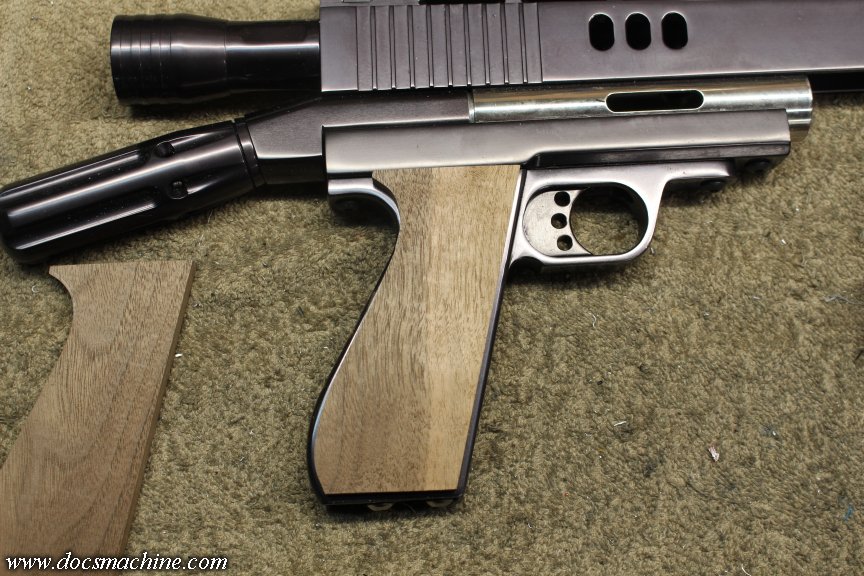
With the outer shape done, we simply profile the edges to smooth up the overall fit.
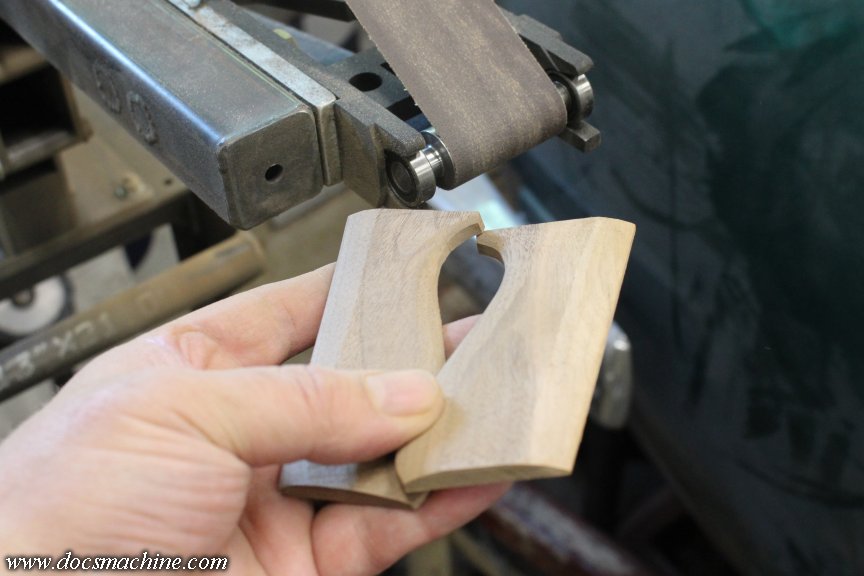
The holes are carefully marked, drilled and countersunk, and once fitted, a few minor touch-ups to the shape, and the curves get hand-sanded smooth.
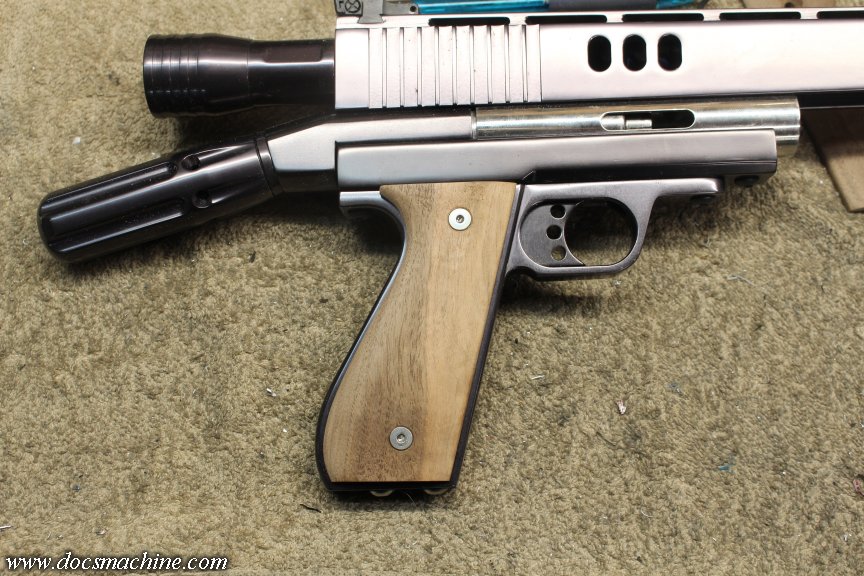
Then they're stained....
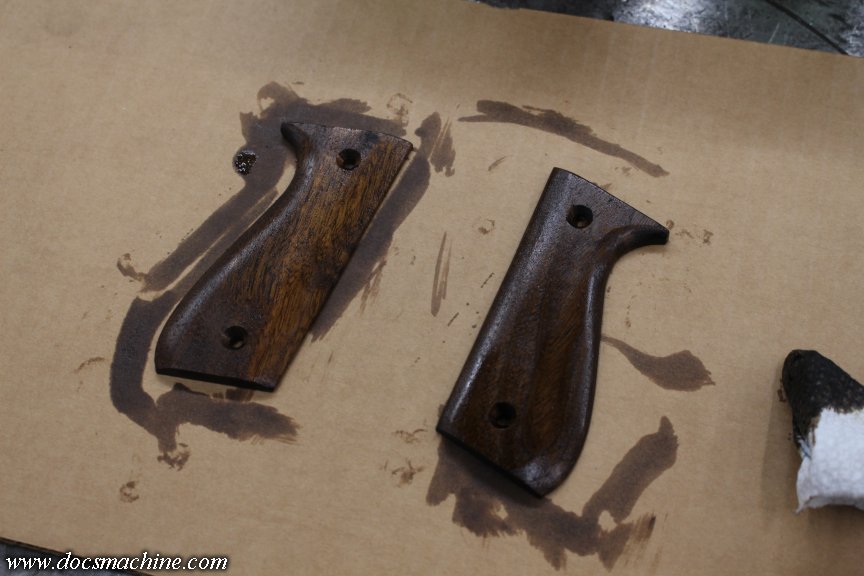
And finally cleared, cured, sanded and cleared again:
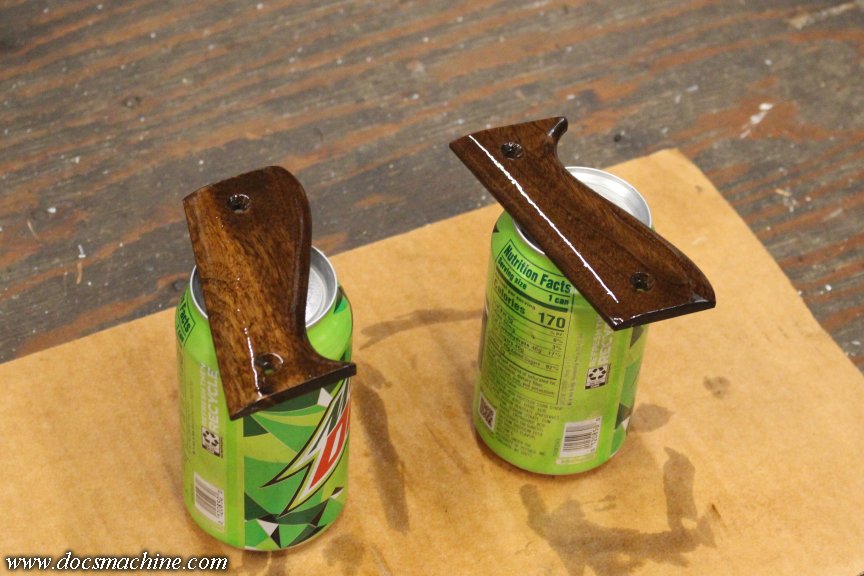
And once fully dry, Voilá!
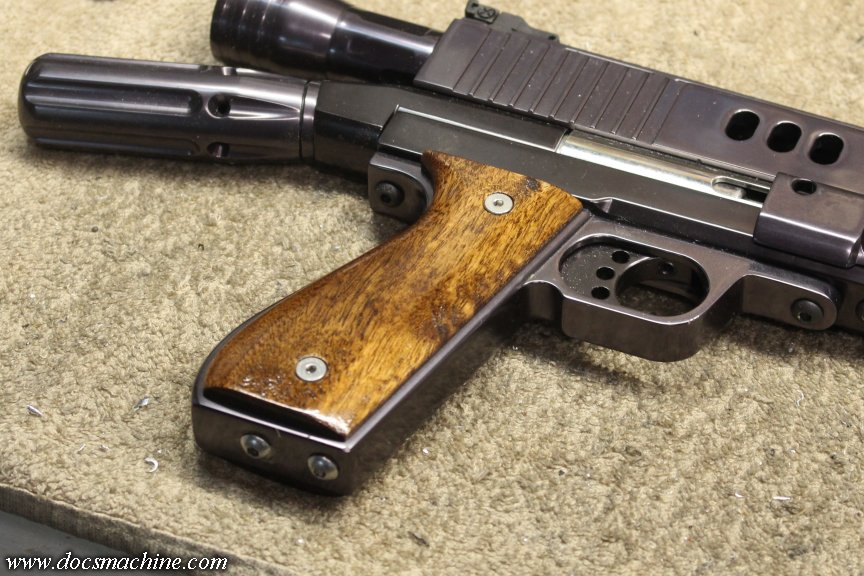
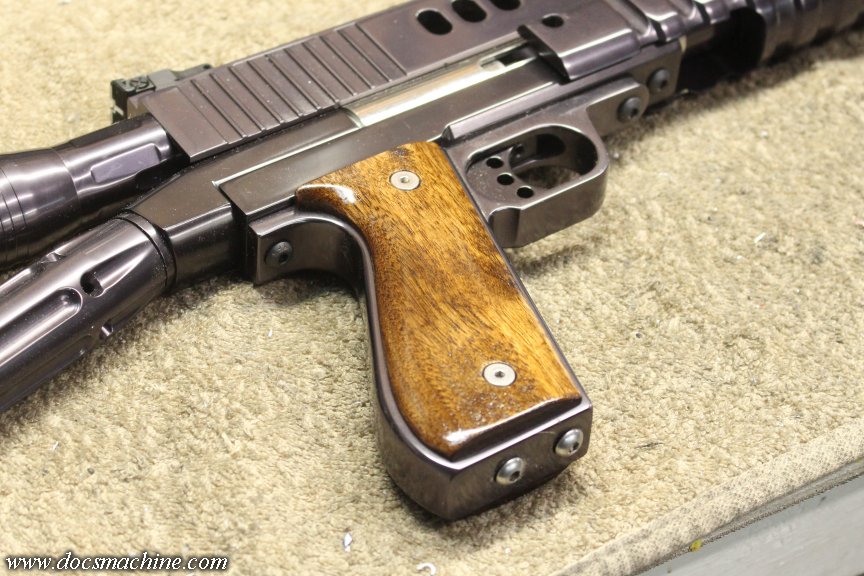
Now if I can just get off my duff and get the anno batch done.
(That's this coming weeks' task.
)
Doc.
So I dug around in my camera cards, and found something from much earlier this year, that I'd been meaning to post after the whole marker is done.
Customer sent in a Carter "Boxgun" stock-classer, and like many Carters, it has a "palm swell" grip. It accepts standard .45 style grip panels, but they don't really fit the profile.
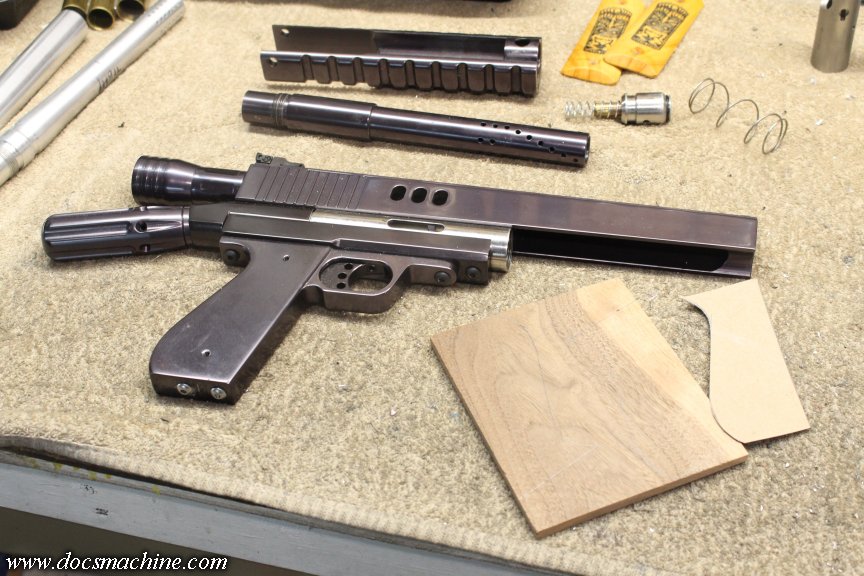
So, I made a cardboard pattern for the grip shape, and traced that to a small slab of Walnut.
This I rough-sawed out with the jigsaw...
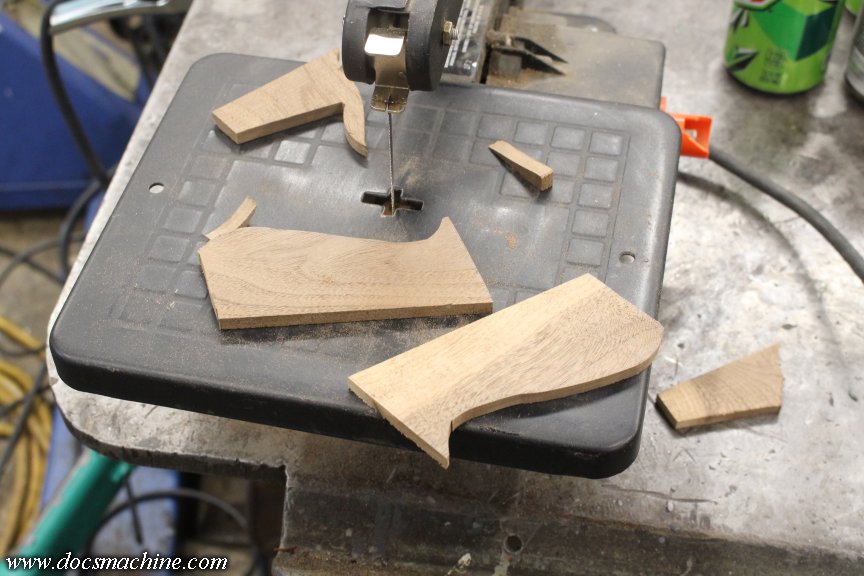
And shaped and smoothed the pair on the belt sander.
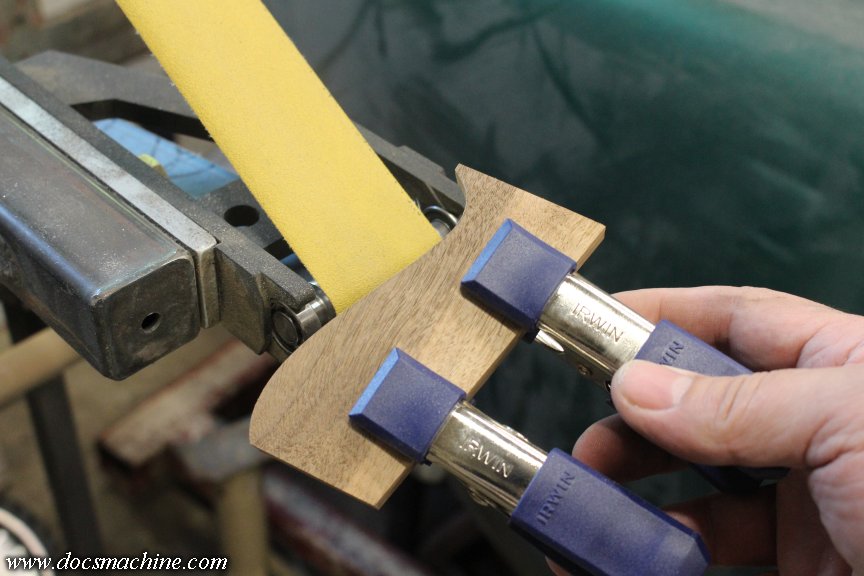
It usually takes a few test-fits and tries to get the shape just right- and the patience to not go too far.

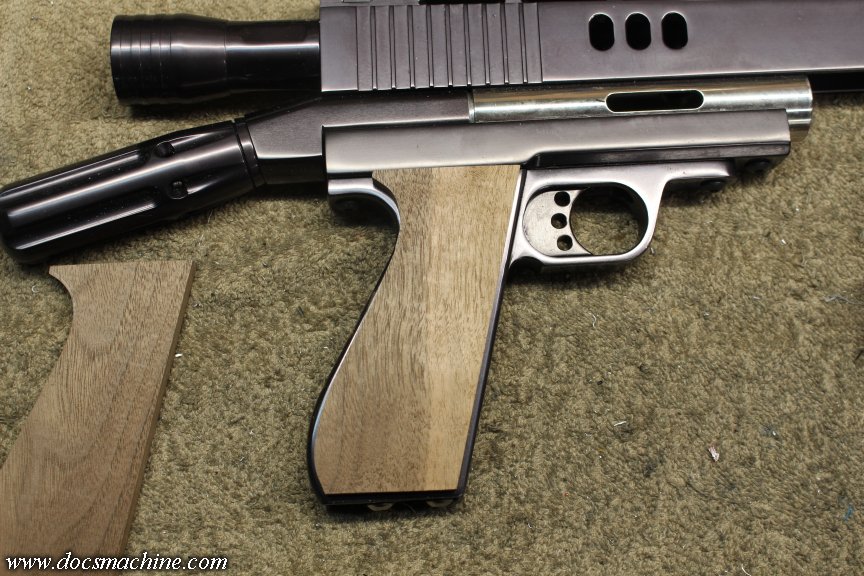
With the outer shape done, we simply profile the edges to smooth up the overall fit.
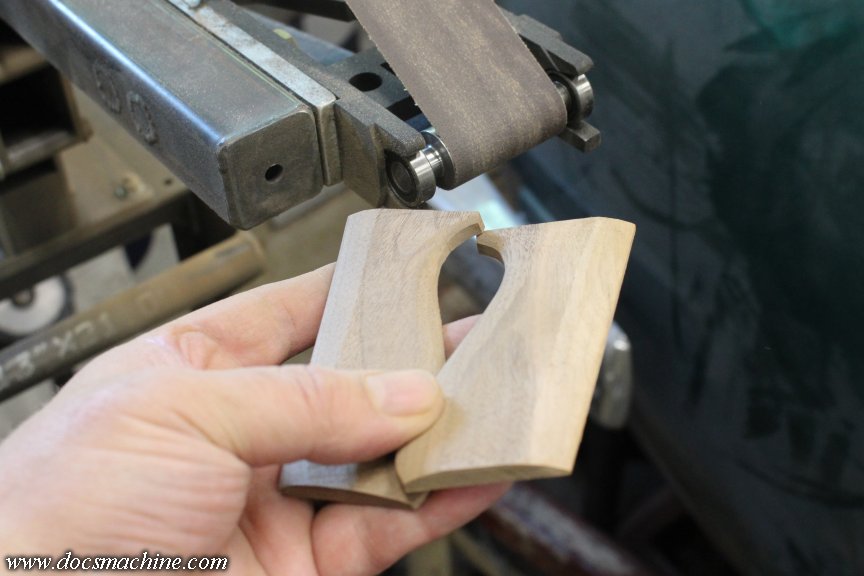
The holes are carefully marked, drilled and countersunk, and once fitted, a few minor touch-ups to the shape, and the curves get hand-sanded smooth.
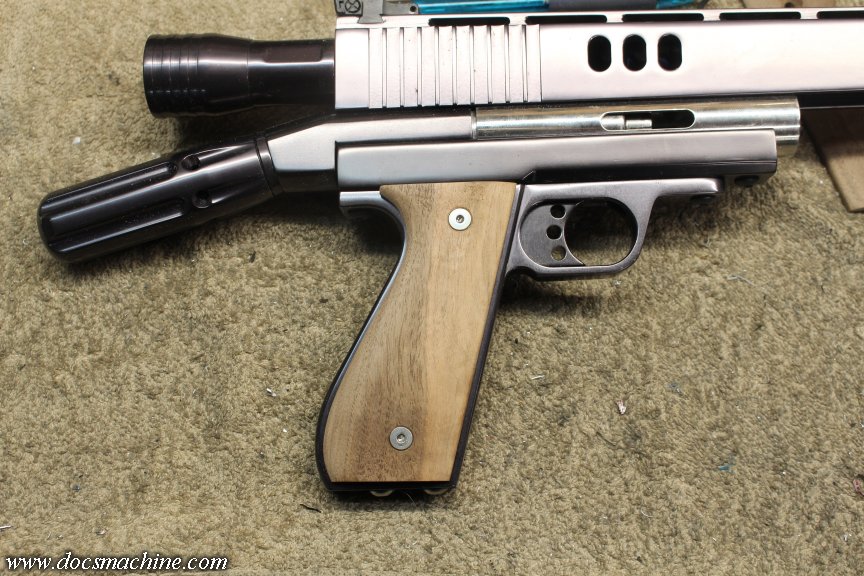
Then they're stained....
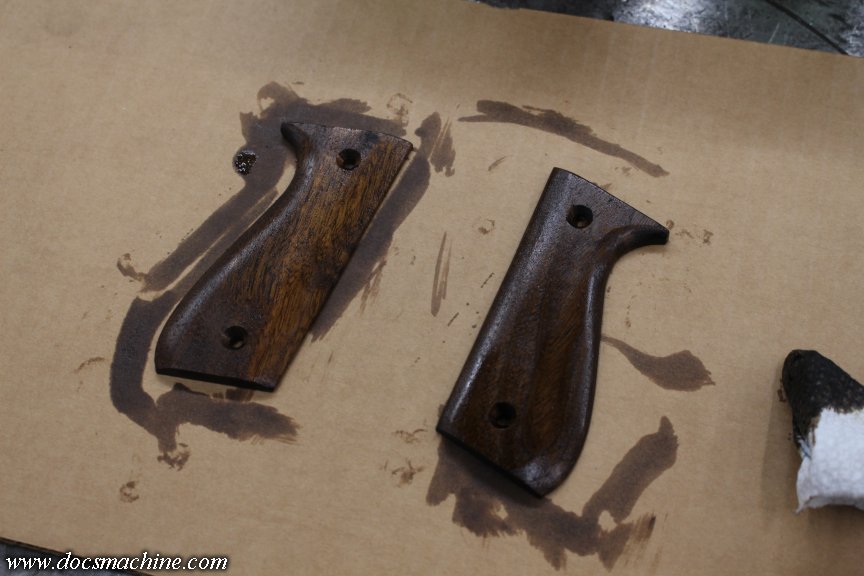
And finally cleared, cured, sanded and cleared again:
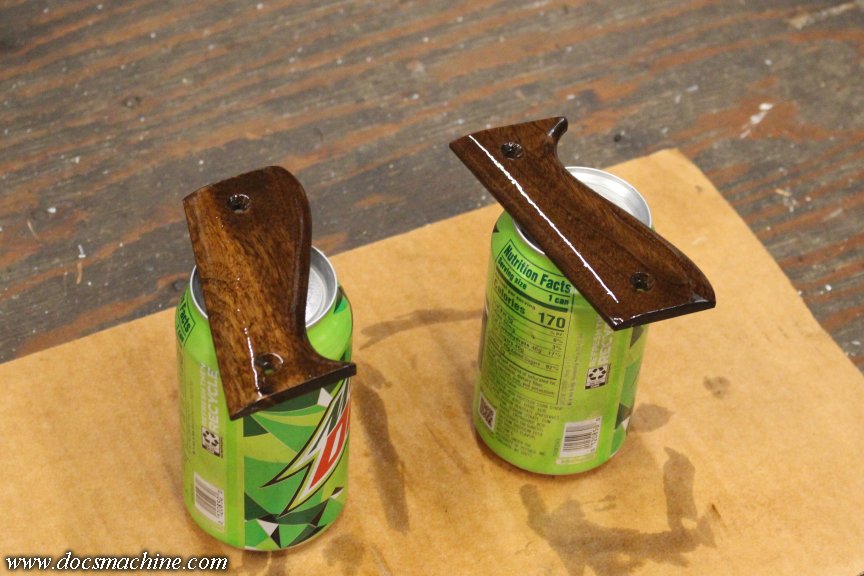
And once fully dry, Voilá!
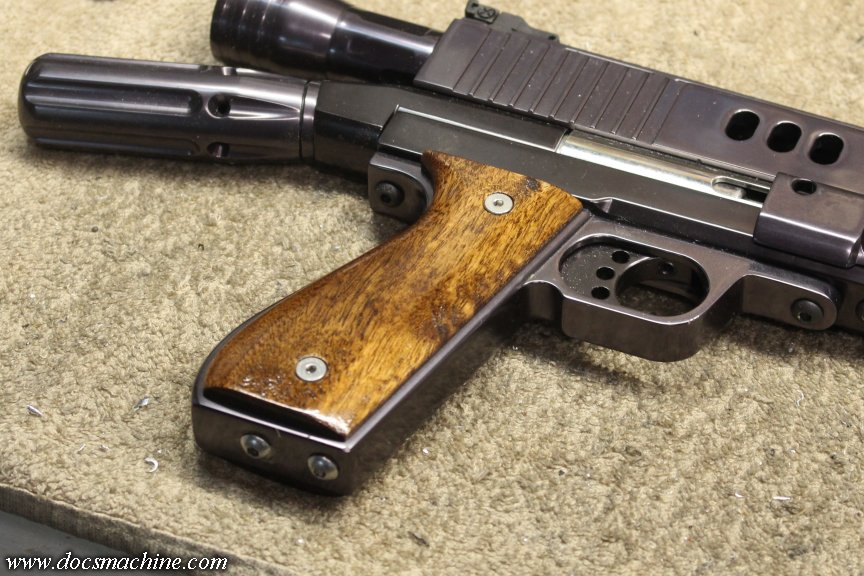
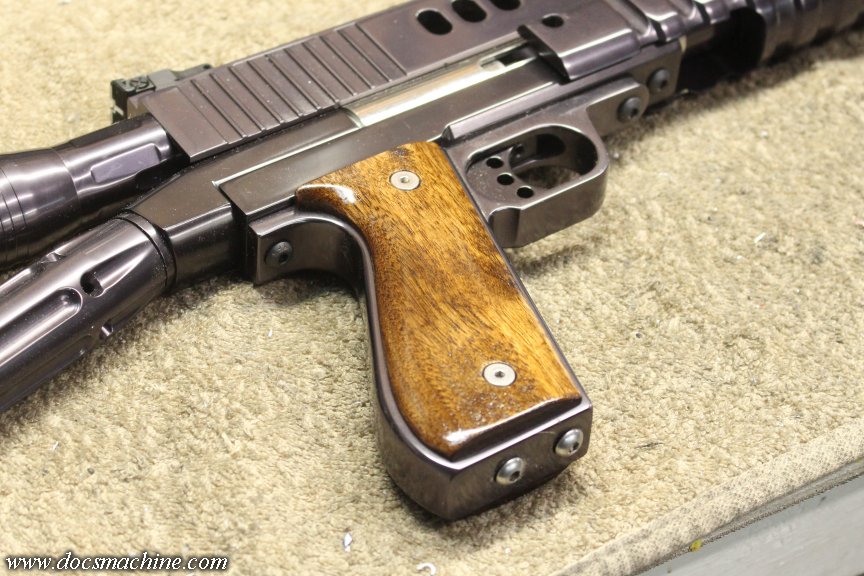
Now if I can just get off my duff and get the anno batch done.


Doc.
Comment