Most of you here know I frequently make Freak backs, especially for those older or less common markers that either never got a factory back, or for whom SP/GOG hasn't made a back in years. Several of you also know there's some markers that can't take a typical Freak back- the way the marker is laid out, there's no way to properly retain the insert.
A common one is Carter pumps, but there are similar issues with Blazers, Raptors, Cobras and a few other guns.
The "big trick" here is that, for a conventional Freak back, there's a common, off-the-shelf heavywall tubing that already has the proper bore size, as supplied. This is a big help to making these things- it keeps me from having to drill out solid bar, or pay for a big run of expensive custom extrusion. The trick to that is, for those guns that need to retain the insert, there's no easy way to add that step, without adding on an extra piece, welding, or drilling the part from solid bar.
I've pondered this issue for some time, and with a little thought and some advice from the Internet At Large® I came up with a solution: Since the end with the step needs to be fully machined anyway, what if I swaged the end of the tube down ? Basically just squished it in a controlled manner to a smaller OD and ID, and then turned the features into it.
A fellow over on HSM posted a pic of a shop-made guillotine swage that I thought would work. I really need to get moving on these parts, if I'm going to do anything with them, so I took some time this morning to build my own version. TL/DR version? It works perfectly.
I started with a hunk of old I-beam out of the scrap piles...
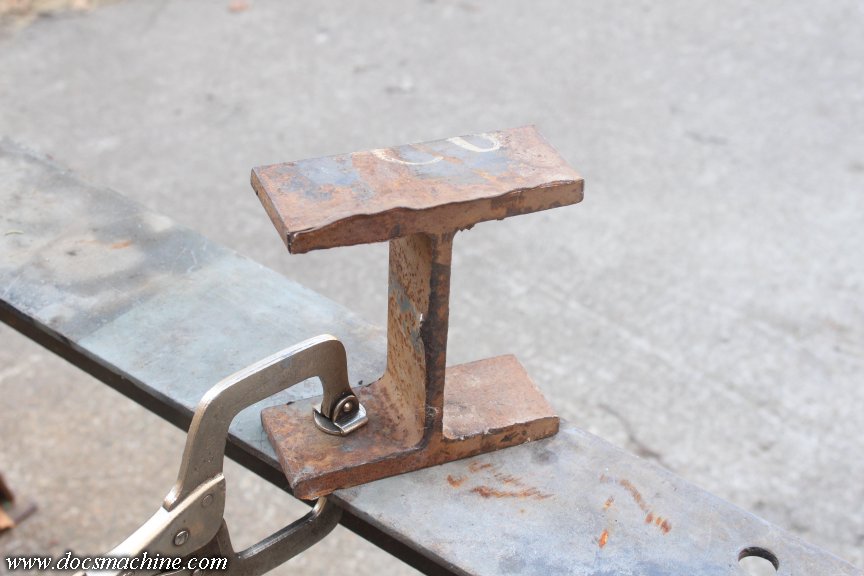
That got ground, sanded and brushed down...
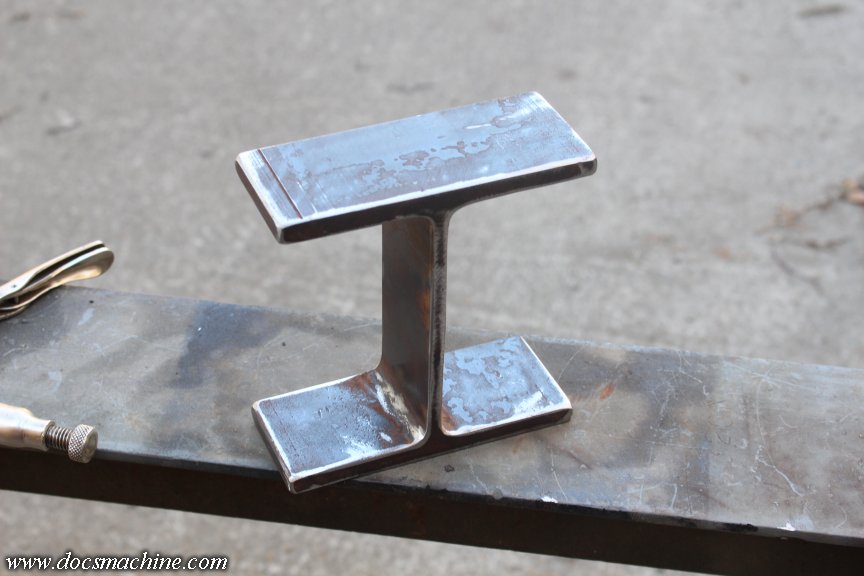
And then bandsawed into pieces.
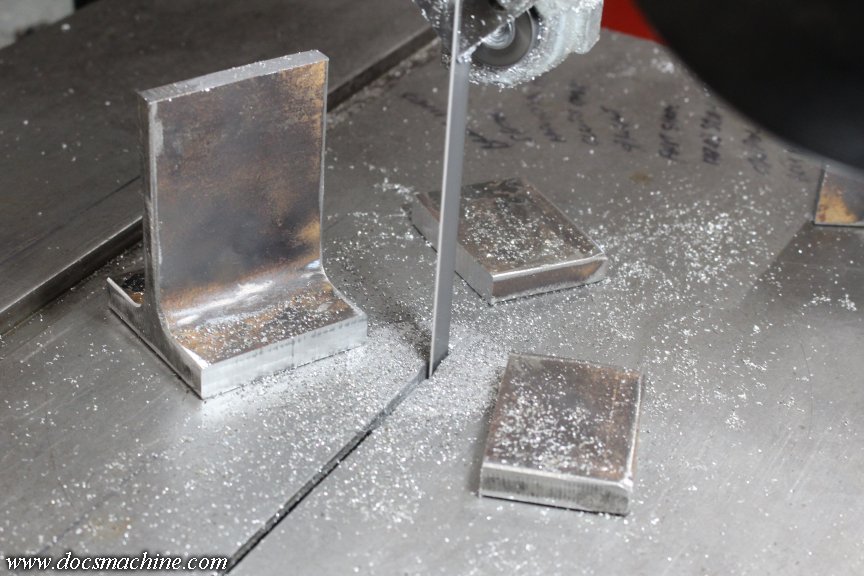
For guides, I dug two chunks of 1" hot-rolled out of the same pile, and slotted each one to fit the web of the I-beam.
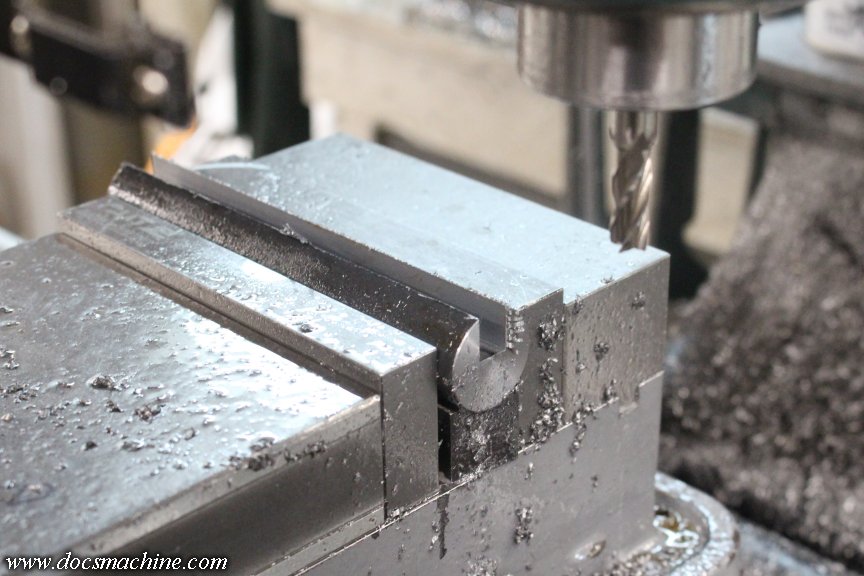
A little bit of fine-tuning with the belt-grinder and a smidge o' TIG, and voila!

That goes into the mill and the operative bore... er, bored.
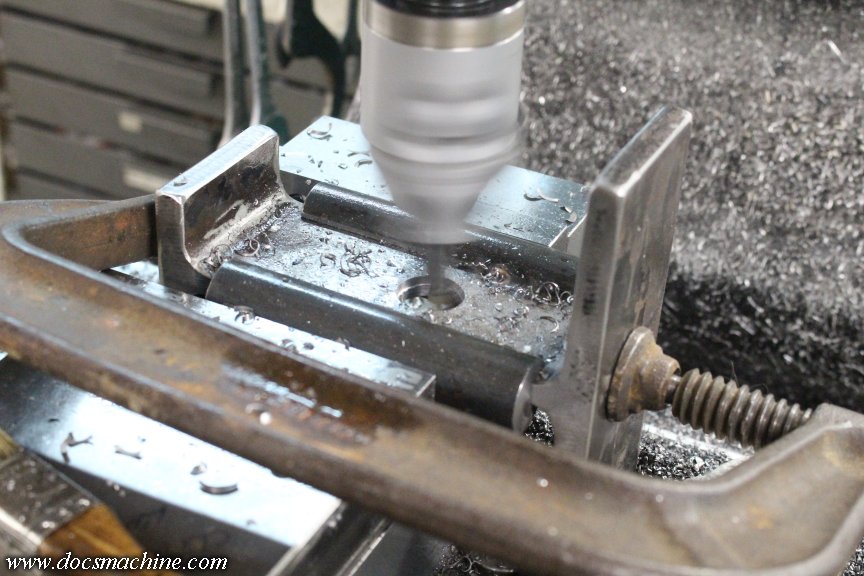
Bit of guesswork there: I wanted to reduce the bore by about .075", so the ID of the dies were cut to about .075" less than the OD of the tubing. The exact number was irrelevant, as long as there was enough material to turn it to the final dimension.
After a little deburring and smoothing, it was time to give it a try. I had some scrap barrels to try it on, so with a little bit of oil brushed on, I stuck the whole mess in the press and gave 'er a squish.
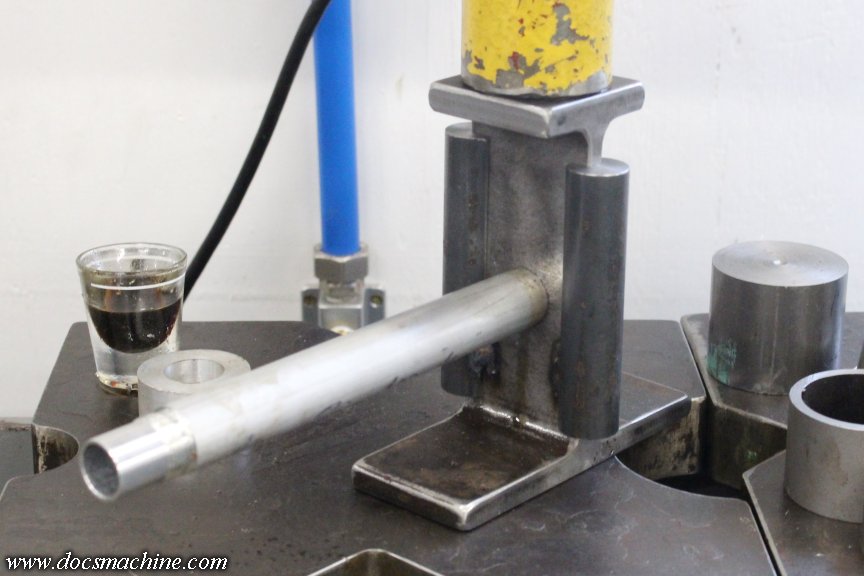
And that, actually, turned out just perfectly.
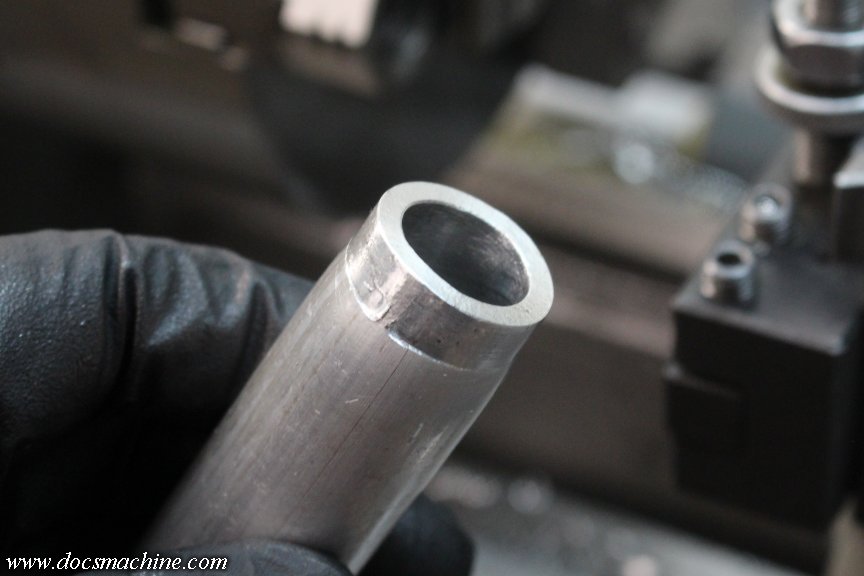
It's not an even squash, I may try going most of the way, turning the tube 90 degrees, and squishing the rest, but even still, that right there is 100% usable.
The bore ended up football shaped, .655" (down from the original nominal .750") across the die parting lines, and .675" vertically. The finished bore needs to be between .695" and maybe .705", so that's perfect.
I chucked it up to see how it turned back to round...
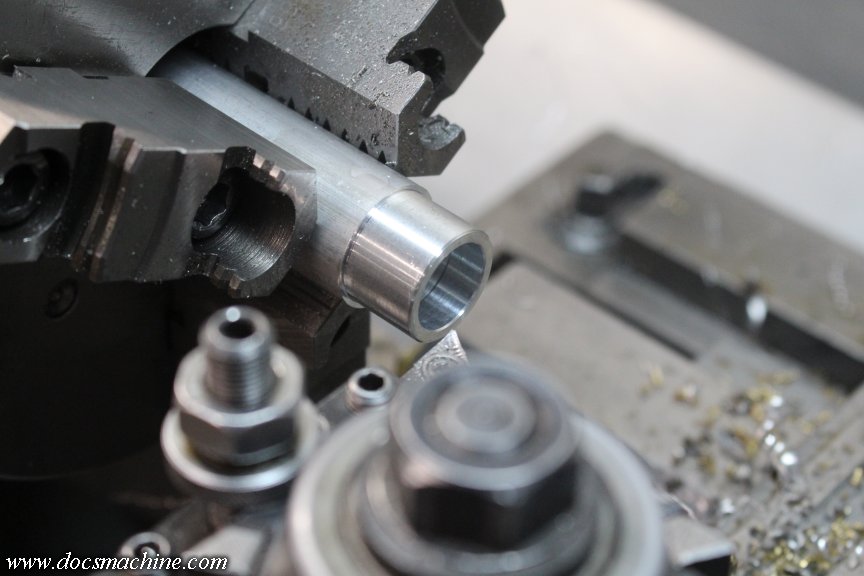
And it appears to have worked perfectly. I turned the bore back to .695", and it retains the insert perfectly.
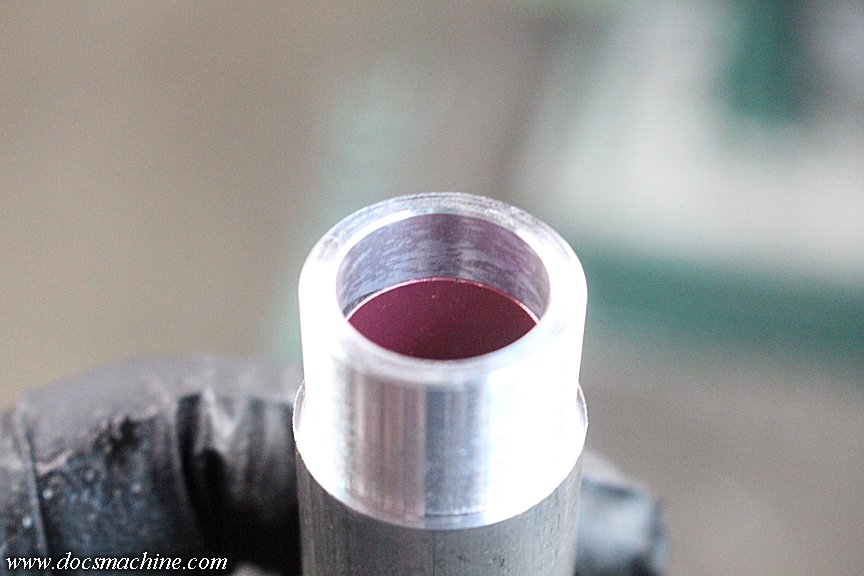
You can see just a touch of eccentricity to the left there, but taking another 5 thou or so, and maybe turning the tube 90 degrees should solve that. Might add a couple short return springs to the swage help make that go a little quicker.
Nice little win to cap off what had been a bit of a tedious week.
Doc.
A common one is Carter pumps, but there are similar issues with Blazers, Raptors, Cobras and a few other guns.
The "big trick" here is that, for a conventional Freak back, there's a common, off-the-shelf heavywall tubing that already has the proper bore size, as supplied. This is a big help to making these things- it keeps me from having to drill out solid bar, or pay for a big run of expensive custom extrusion. The trick to that is, for those guns that need to retain the insert, there's no easy way to add that step, without adding on an extra piece, welding, or drilling the part from solid bar.
I've pondered this issue for some time, and with a little thought and some advice from the Internet At Large® I came up with a solution: Since the end with the step needs to be fully machined anyway, what if I swaged the end of the tube down ? Basically just squished it in a controlled manner to a smaller OD and ID, and then turned the features into it.
A fellow over on HSM posted a pic of a shop-made guillotine swage that I thought would work. I really need to get moving on these parts, if I'm going to do anything with them, so I took some time this morning to build my own version. TL/DR version? It works perfectly.

I started with a hunk of old I-beam out of the scrap piles...
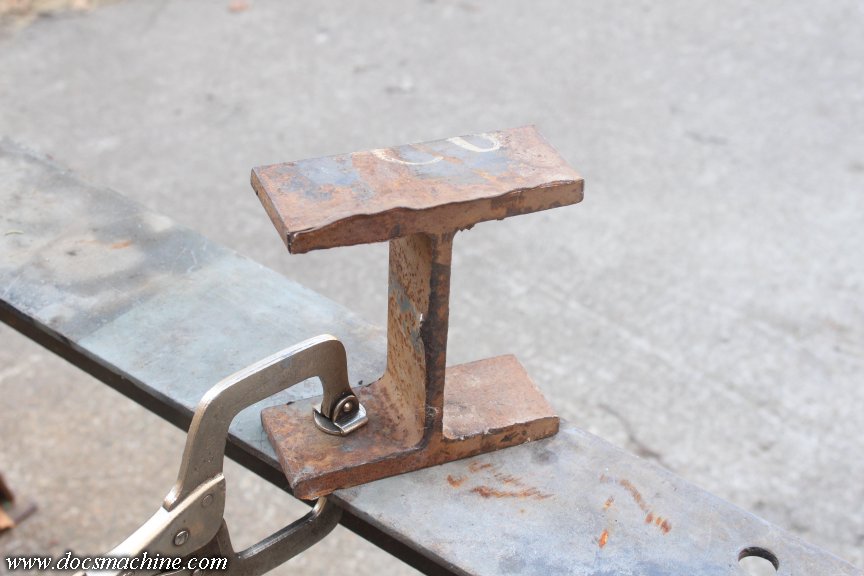
That got ground, sanded and brushed down...
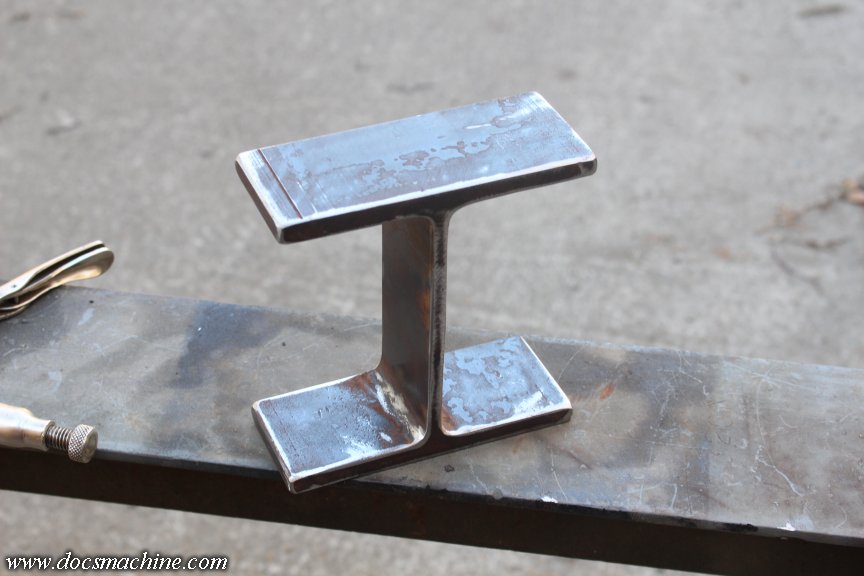
And then bandsawed into pieces.
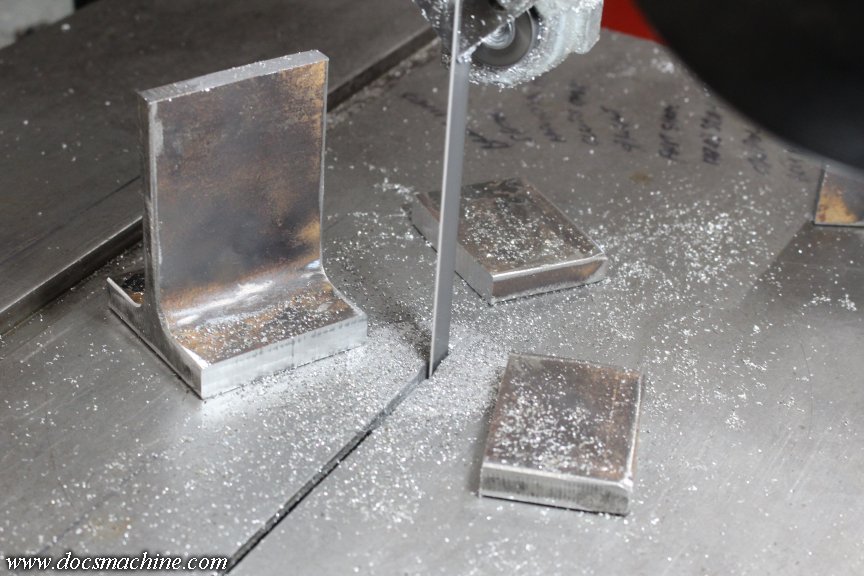
For guides, I dug two chunks of 1" hot-rolled out of the same pile, and slotted each one to fit the web of the I-beam.
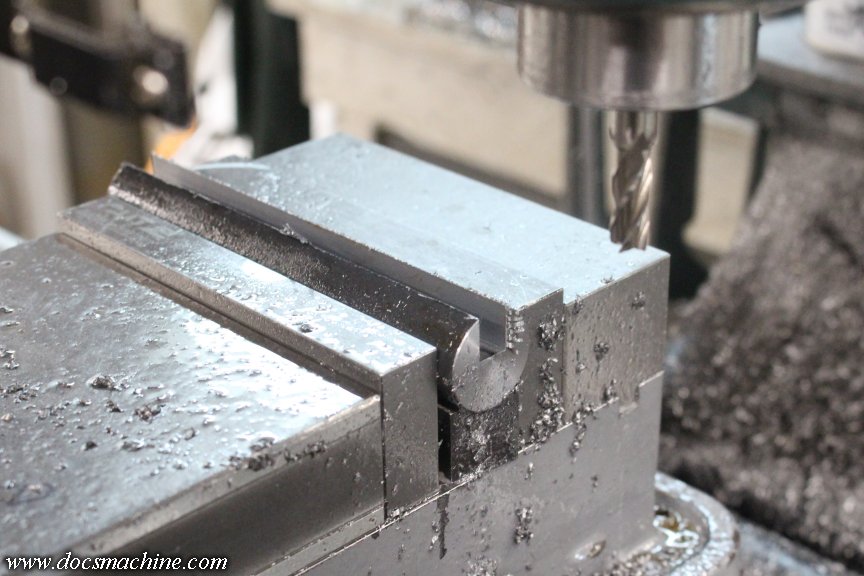
A little bit of fine-tuning with the belt-grinder and a smidge o' TIG, and voila!

That goes into the mill and the operative bore... er, bored.
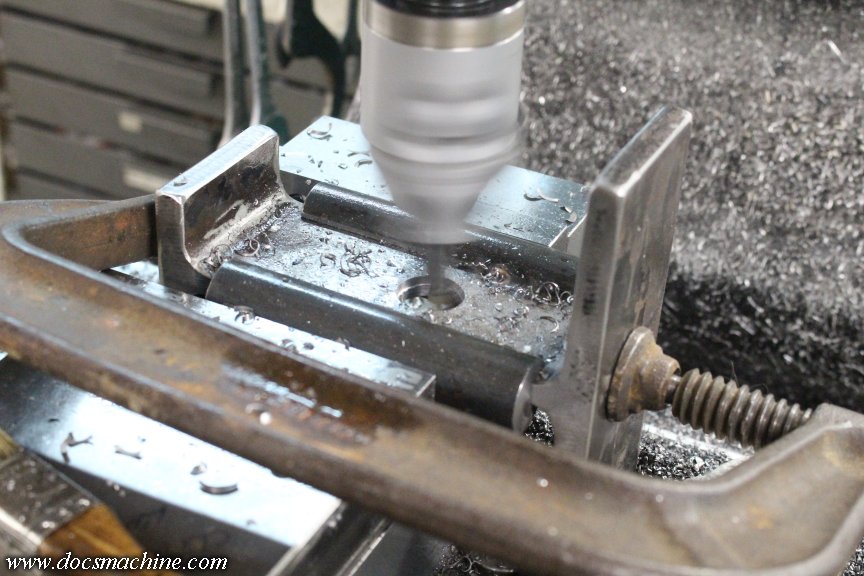
Bit of guesswork there: I wanted to reduce the bore by about .075", so the ID of the dies were cut to about .075" less than the OD of the tubing. The exact number was irrelevant, as long as there was enough material to turn it to the final dimension.
After a little deburring and smoothing, it was time to give it a try. I had some scrap barrels to try it on, so with a little bit of oil brushed on, I stuck the whole mess in the press and gave 'er a squish.
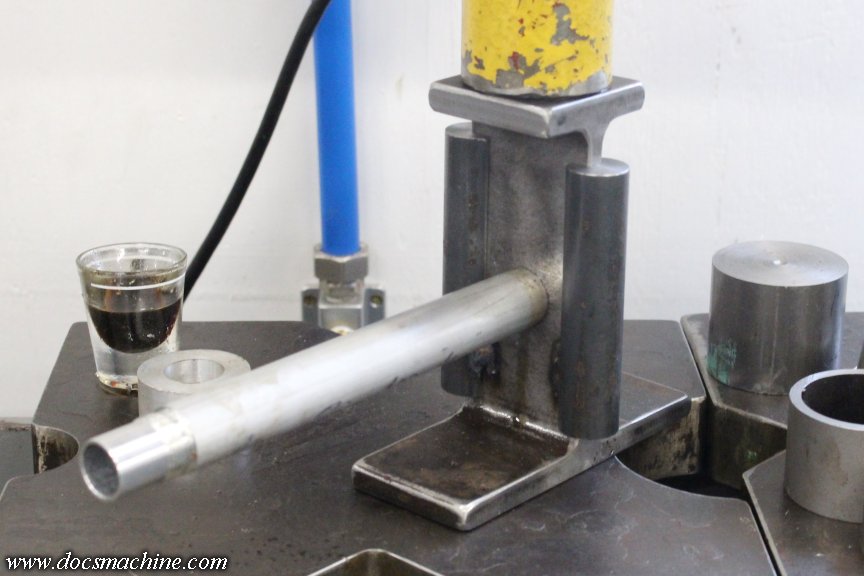
And that, actually, turned out just perfectly.
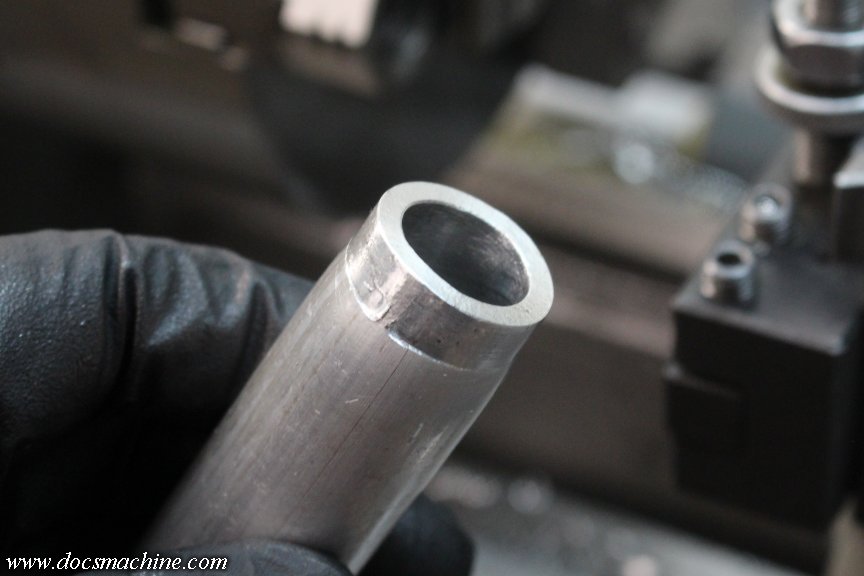
It's not an even squash, I may try going most of the way, turning the tube 90 degrees, and squishing the rest, but even still, that right there is 100% usable.
The bore ended up football shaped, .655" (down from the original nominal .750") across the die parting lines, and .675" vertically. The finished bore needs to be between .695" and maybe .705", so that's perfect.
I chucked it up to see how it turned back to round...
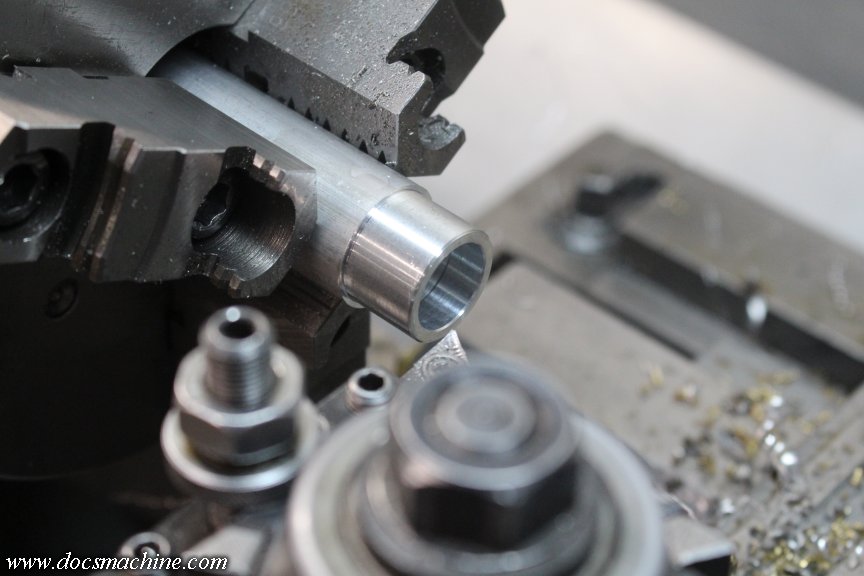
And it appears to have worked perfectly. I turned the bore back to .695", and it retains the insert perfectly.
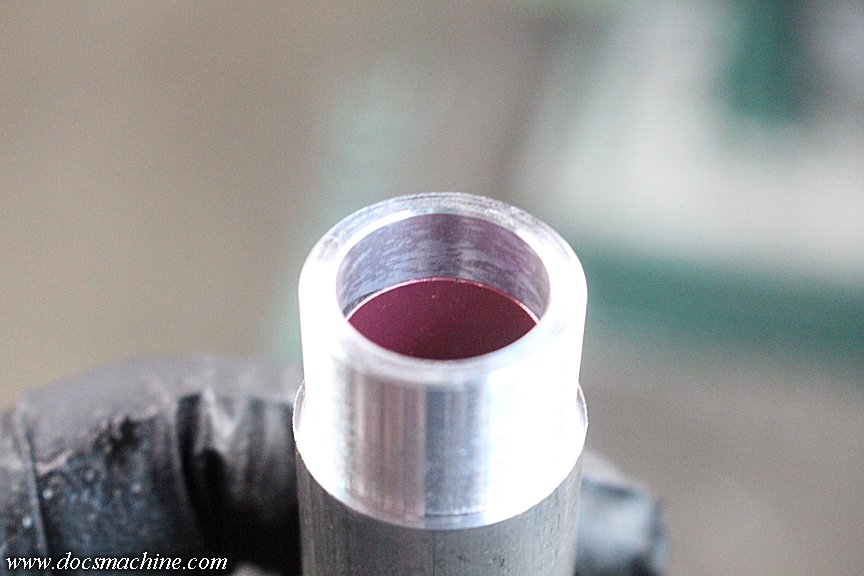
You can see just a touch of eccentricity to the left there, but taking another 5 thou or so, and maybe turning the tube 90 degrees should solve that. Might add a couple short return springs to the swage help make that go a little quicker.
Nice little win to cap off what had been a bit of a tedious week.

Doc.
Comment