I'd like to let you ladies and gents in on a little secret. A dirty secret I've been carefully guarding for many, many years now. Are you ready for this?
I make parts for paintball guns.
Yeah, I'm sure that's a lot to take in; if you need to, go lie down, have a stiff drink, breathe into a paper bag if you need to. Or even a half-full Doritos bag, I don't judge.
The other side of that dirty little secret is that for all these years I've been a manual machine shop. That is, I make my parts on plain manual engine lathes, Bridgeport style manual mills, drill presses, and big freakin' hammers. (The latter mostly used for "fixing" Ions.
) I've contracted out to several CNC production shops for many of my products over the years, but a lot of what I've made, I made basically by hand, one crank of the handle at a time.
Now, trying not to get too windy here, one of the biggest problems I have with those outside shops is the volume of parts I make. A typical production CNC shop wants to see orders of 5,000 and 10,000 parts. But while I'd love to have some products that sell by the thousands, I don't. Most of my stuff sells in the 50 to 200 range. And while I can occasionally find a shop that will make a batch that small, that's small enough that I get kicked to the back burner if the shop gets busy.
And, you know what's happened since Covid hit? All those shops have either had to cut way back (time, people, pay, etc.) or are taking on the demand from shops that had to pare back.
One of my best suppliers did this. He took on a ton of work from outside shops, and my little batches got shoved to the bottom of the list. I ordered over $8K- my cost- in five different parts almost seventeen months ago. As of six weeks ago, I finally got the second half of the FIRST of them. Some of you gents wondering where my Tanto barrels are? There's your answer. I beg, I plead, I wave money, and I get told I'm "next on the list" and still I wait. And wait, and wait.
Earlier this summer, after the one-year mark came and went, I finally decided to do something about it. Something I've been planning to do and working towards for better than five years now.
I bought my own goddam machine.
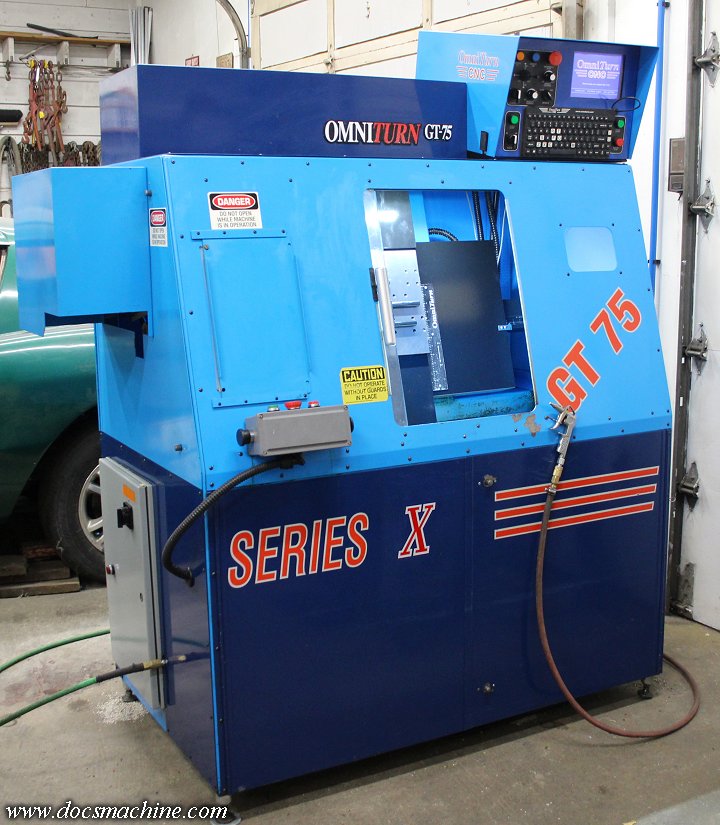
This was not a step I took lightly. My little biz here has always been very low profit, and generally operated off a tattered and frayed shoestring budget. I put myself rather badly in debt over this, and worse, the day it arrived, I had no idea how to actually operate it.
Worse still, here in downtown backwater Left Armpit, Alaska, people that DO know how to use it are few and far between. So far between, they basically don't exist. Teaching myself to use a professional-quality CNC turning center, when as of a few years before, I'd never so much as pushed the "start" button on so much as a cheap 3D printer, has been a great deal* (in this case, meaning "very little") fun.
However, all that woe-is-me crap aside, I have it up and running, I know just enough of how to program it that I only crash it a few dozen a day, and I've made my first small batch of what are basically test parts.
And for you bored sorts, I made videos of doing so.
Now, this is not by any stretch of the imagination the "right" way to make parts, or even how I normally made them. Actually, to be honest this is all kind of a clusterflux.
But again, it's just a test part- A fairly simple piece that was just a drawing I had on hand to give me something to practice programming. But, once I had the code more or less settled out (mostly less) I hated to "waste" the effort, so I found a bar of material, chopped it up, and made a small run out of it.
The "right" way would have been to have the entire piece run on the CNC, but I'm still short some crucial tooling, and for such a small run, it wasn't worth buying it just yet, nor setting it up. So, I wound up taking, including learning-to-program time, waiting-on-tools time, and working-on-paying-jobs time, approximately five weeks, and four different machines, to make a whopping thirty parts.
It'll get better from here. (I hope.
)
So, Part One: After chopping a chunk of 1" bar to length with an Evolution style saw, each one was faced to length and drilled on the turret lathe:
Part Two, running each one through the CNC lathe. For those of you with more extensive G-code experience, don't laugh too hard- six weeks ago I couldn't have done any of that.
And finally, Part Three, knurling each one, and chamfering the edges where the knurling rolled the metal over a bit.
The next part, I hope to make a lot more, like 200+. I can't make Tantos yet, they're too long for this machine. But the pro shop has, once again, promised them "shortly". (Where's the "rolls eyes" smiley?) But I still have some old favorites to bring back, a new anno shop that's promising me much better turnarounds (I had one shop close on me last year, taking nearly 200 parts into limbo with it) and overall hopefully more parts and faster production.
Doc.
I make parts for paintball guns.
Yeah, I'm sure that's a lot to take in; if you need to, go lie down, have a stiff drink, breathe into a paper bag if you need to. Or even a half-full Doritos bag, I don't judge.
The other side of that dirty little secret is that for all these years I've been a manual machine shop. That is, I make my parts on plain manual engine lathes, Bridgeport style manual mills, drill presses, and big freakin' hammers. (The latter mostly used for "fixing" Ions.

Now, trying not to get too windy here, one of the biggest problems I have with those outside shops is the volume of parts I make. A typical production CNC shop wants to see orders of 5,000 and 10,000 parts. But while I'd love to have some products that sell by the thousands, I don't. Most of my stuff sells in the 50 to 200 range. And while I can occasionally find a shop that will make a batch that small, that's small enough that I get kicked to the back burner if the shop gets busy.
And, you know what's happened since Covid hit? All those shops have either had to cut way back (time, people, pay, etc.) or are taking on the demand from shops that had to pare back.
One of my best suppliers did this. He took on a ton of work from outside shops, and my little batches got shoved to the bottom of the list. I ordered over $8K- my cost- in five different parts almost seventeen months ago. As of six weeks ago, I finally got the second half of the FIRST of them. Some of you gents wondering where my Tanto barrels are? There's your answer. I beg, I plead, I wave money, and I get told I'm "next on the list" and still I wait. And wait, and wait.
Earlier this summer, after the one-year mark came and went, I finally decided to do something about it. Something I've been planning to do and working towards for better than five years now.
I bought my own goddam machine.
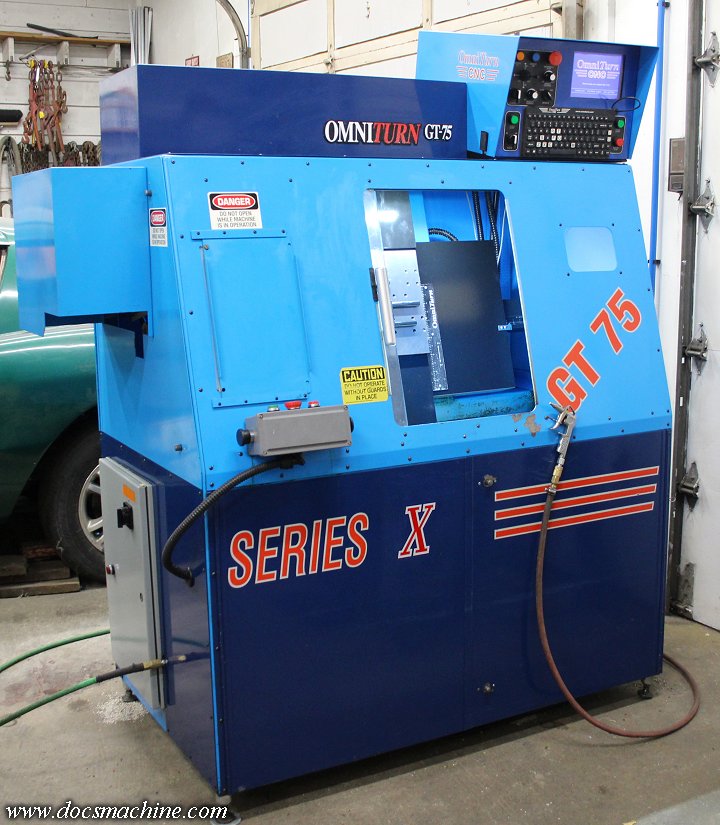
This was not a step I took lightly. My little biz here has always been very low profit, and generally operated off a tattered and frayed shoestring budget. I put myself rather badly in debt over this, and worse, the day it arrived, I had no idea how to actually operate it.

Worse still, here in downtown backwater Left Armpit, Alaska, people that DO know how to use it are few and far between. So far between, they basically don't exist. Teaching myself to use a professional-quality CNC turning center, when as of a few years before, I'd never so much as pushed the "start" button on so much as a cheap 3D printer, has been a great deal* (in this case, meaning "very little") fun.
However, all that woe-is-me crap aside, I have it up and running, I know just enough of how to program it that I only crash it a few dozen a day, and I've made my first small batch of what are basically test parts.
And for you bored sorts, I made videos of doing so.

Now, this is not by any stretch of the imagination the "right" way to make parts, or even how I normally made them. Actually, to be honest this is all kind of a clusterflux.

The "right" way would have been to have the entire piece run on the CNC, but I'm still short some crucial tooling, and for such a small run, it wasn't worth buying it just yet, nor setting it up. So, I wound up taking, including learning-to-program time, waiting-on-tools time, and working-on-paying-jobs time, approximately five weeks, and four different machines, to make a whopping thirty parts.

It'll get better from here. (I hope.

So, Part One: After chopping a chunk of 1" bar to length with an Evolution style saw, each one was faced to length and drilled on the turret lathe:
Part Two, running each one through the CNC lathe. For those of you with more extensive G-code experience, don't laugh too hard- six weeks ago I couldn't have done any of that.

And finally, Part Three, knurling each one, and chamfering the edges where the knurling rolled the metal over a bit.
The next part, I hope to make a lot more, like 200+. I can't make Tantos yet, they're too long for this machine. But the pro shop has, once again, promised them "shortly". (Where's the "rolls eyes" smiley?) But I still have some old favorites to bring back, a new anno shop that's promising me much better turnarounds (I had one shop close on me last year, taking nearly 200 parts into limbo with it) and overall hopefully more parts and faster production.
Doc.
Comment