
While I still had the plain vise set up, I nibbled down a bit of the extra at the peak of the front extension, to make the hand-filing a little easier.
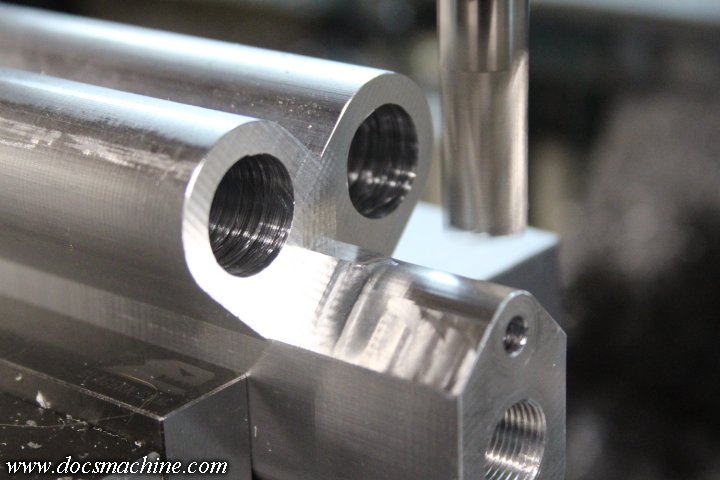
And now, the big step: barrel threads! First we bore to size...
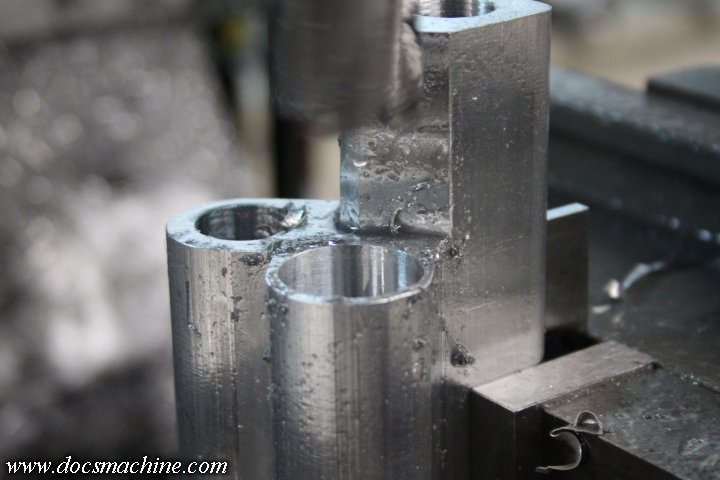
Then thread!
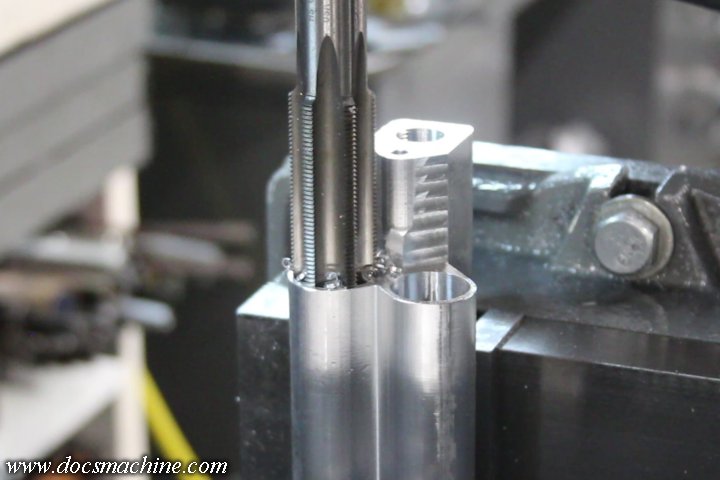
Do that approximately sixty-three more times, at least according to my shoulders, and they're finally ready for barrels!
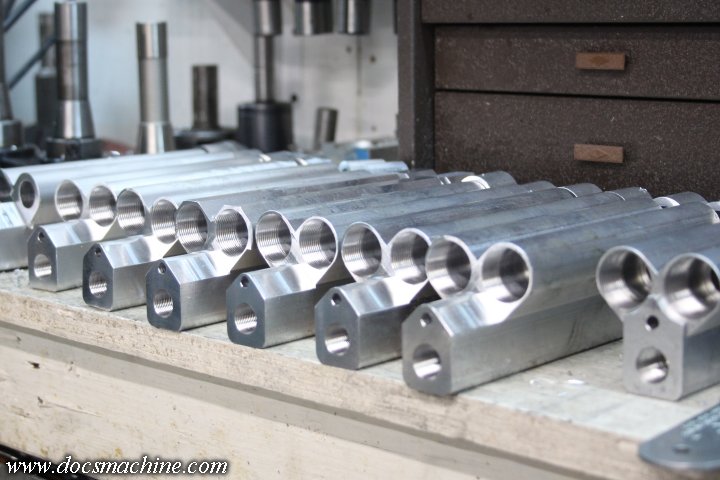
Like so!

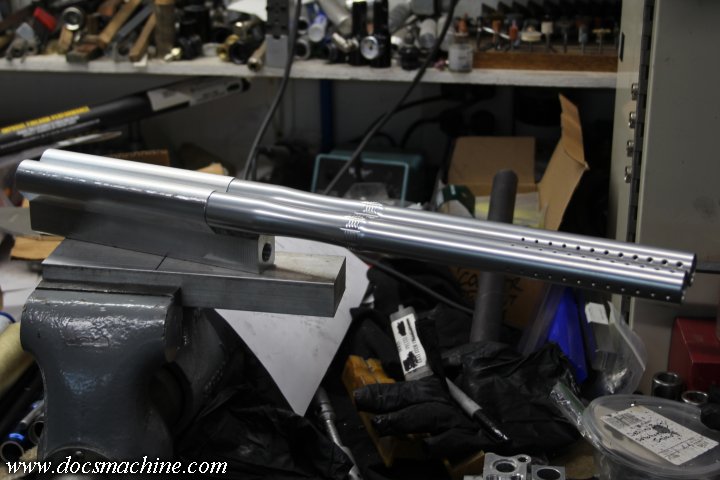
Now, the next step is drilling and finishing the valve bores, so I spent a few minutes trying that out on the Evil Twin (as shown in its thread.) I was able to establish the measurements I needed, so hopefully the rest will go fairly smoothly.
Keep standing by!

Doc.
Leave a comment: